Dutch Magnetics has an advanced solution designed specifically for separating ultrafine fractions in recycling processes with the eccentric Eddy Current Separator.
In recycling processes, the demand for recovering ultrafine fractions from complex material streams has steadily increased. Ultrafine materials, often overlooked by traditional separation methods, contain valuable raw materials that can contribute significantly to the circular economy. Dutch Magnetics is addressing this challenge with the Eccentric Eddy Current Separator, aiming to improve fine particle recovery while maintaining high separation efficiency.
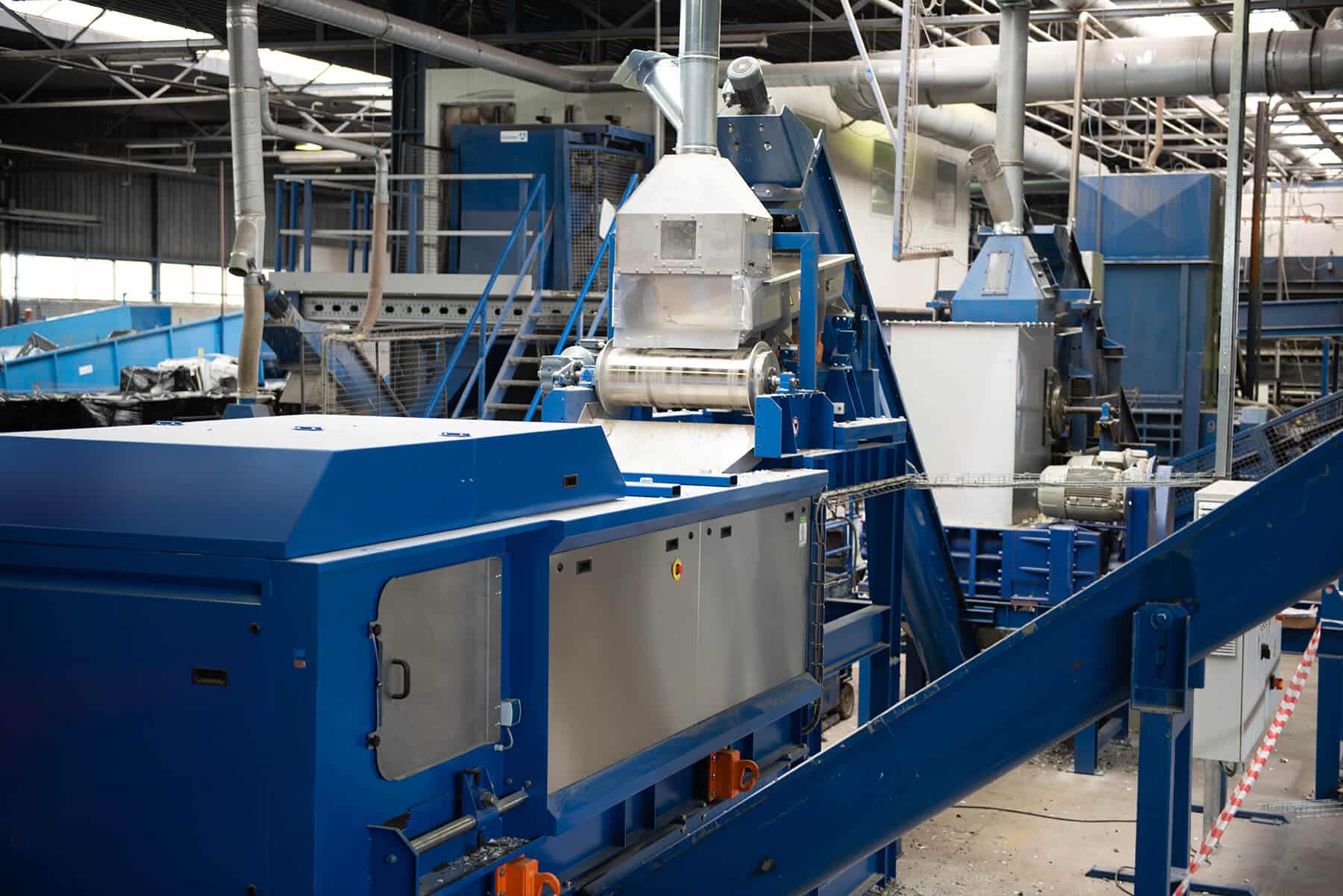
Working principle
The working principle of an eddy current separation system is based on the difference in electrical conductivity of non-ferrous metals. A conveyor leads the product flow to a magnetic rotor rotating at high speed. This magnetic rotor produces a rapidly changing magnetic field, generating an electric current in the electrically conductive nonferrous metals. This (induction) voltage produces a magnetic field opposite to that of the rotor causing non-ferrous metals to be repelled by a Lorentz force. Thus, it is the Lorentz force that repels an electrically conductive particle from the rotating magnet rotor.
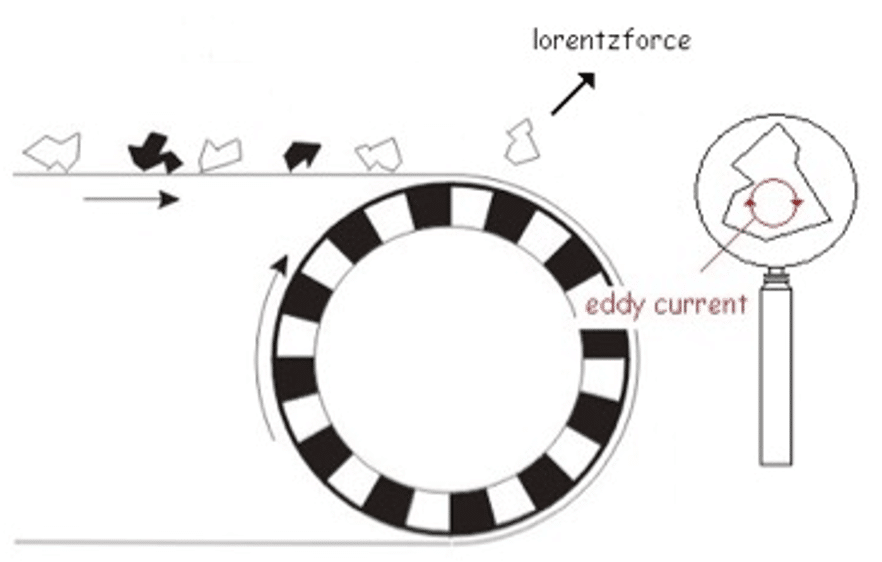
The Lorentz force and the vector of the Lorentz force, together with the specific gravity of the particle to be repelled, determine the repulsive parabola. The better the electrical conductivity of a nonferrous metal particle, the higher the Lorentz force (repulsive force). The higher the specific gravity the sooner the particle will want to fall down.
The ratio of the electrical conductivity to the density of the non-ferrous metal in question is called the separation ratio; it is shown in the chart below.
CHARACTERISTIC PARAMETER FOR EDDY-CURRENT SEPARATION. | |||
Non-ferrous metal: | Electr. Conductivity: | Density: | Ratio: |
Aluminum | 0,35 | 2,7 | 13 |
Copper | 0,59 | 8,9 | 6,7 |
Silver | 0,63 | 10,5 | 6 |
Zinc | 0,17 | 7,1 | 2,4 |
Brass | 0,14 | 8,5 | 1,7 |
Tin | 0,09 | 7,3 | 1,2 |
Lead | 0,05 | 11,3 | 0,4 |
Key Features of the Eccentric Eddy Current Separator
Eccentric Rotor Design
The eccentric Eddy Current Separator is characterized by its innovative rotor design. The eccentric positioning of the magnetic rotor in the drum adds a unique element to the separation process, allowing better control of the particle trajectory and improving separation efficiency. “The rotor has 104 magnets along its circumference and rotates at a speed of 3,600 rpm, generating an impressive frequency of 1.56 kHz. High rotor frequency is essential to effectively impact very small non-ferromagnetic particles. The magnetic rotor is positioned at 8 degrees in its sheath allowing particles to be accelerated in the correct directions.
Variable Rotor
One of the most striking features of this separator is the ability to control the rotational speed of the eccentric rotor. This flexibility allows operators to optimize the separation process based on the specific characteristics of the material being processed, thereby efficiently recovering ultrafine fractions. Depending on your product, the 104x machine allows for counterclockwise rotation of the rotor to better impound non ferrous particles.
Targeted ultrafine fractions
The eccentric Eddy Current Separator is designed to target particles in the ultrafine range, including particles smaller than 8 mm. This capability sets it apart from conventional eddy current separators, making it a valuable asset for applications where precision in separation is paramount.
Adjustable parameters
To handle different material compositions, the machine can be set and separator calibrated to your product.
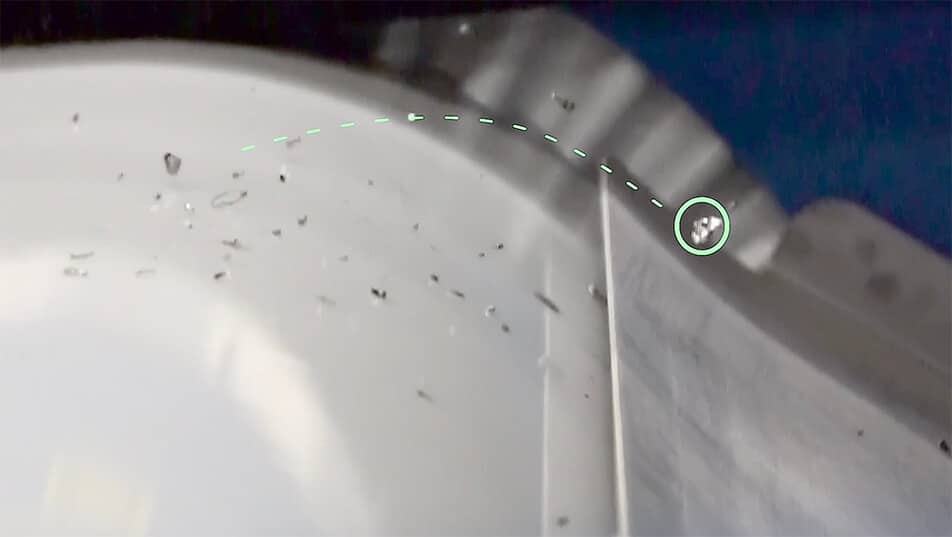
Machine setup of the Eccentric Eddy Current Separator
Variables:
- Belt speed.
- Rotor speed.
- Rotor rotation direction.
- Position of the separation partition.
- Inclination angle of the separation partition.
- Distribution and layer thickness of the material flow on the conveyor belt (EC).
1] Belt speed
The belt speed determines the rejection parabola of the material particles, the residence time in the magnetic field and the air resistance experienced by the material.
2] Rotor speed
The rotor speed determines not only the Lorentz force but also the vector of the Lorentz force. The lower the vector the flatter the rejection parabola.
It is important to look for an ideal relationship between the repulsion force and the repulsion parabola. See graphical representations below showing the importance of correct adjustment:
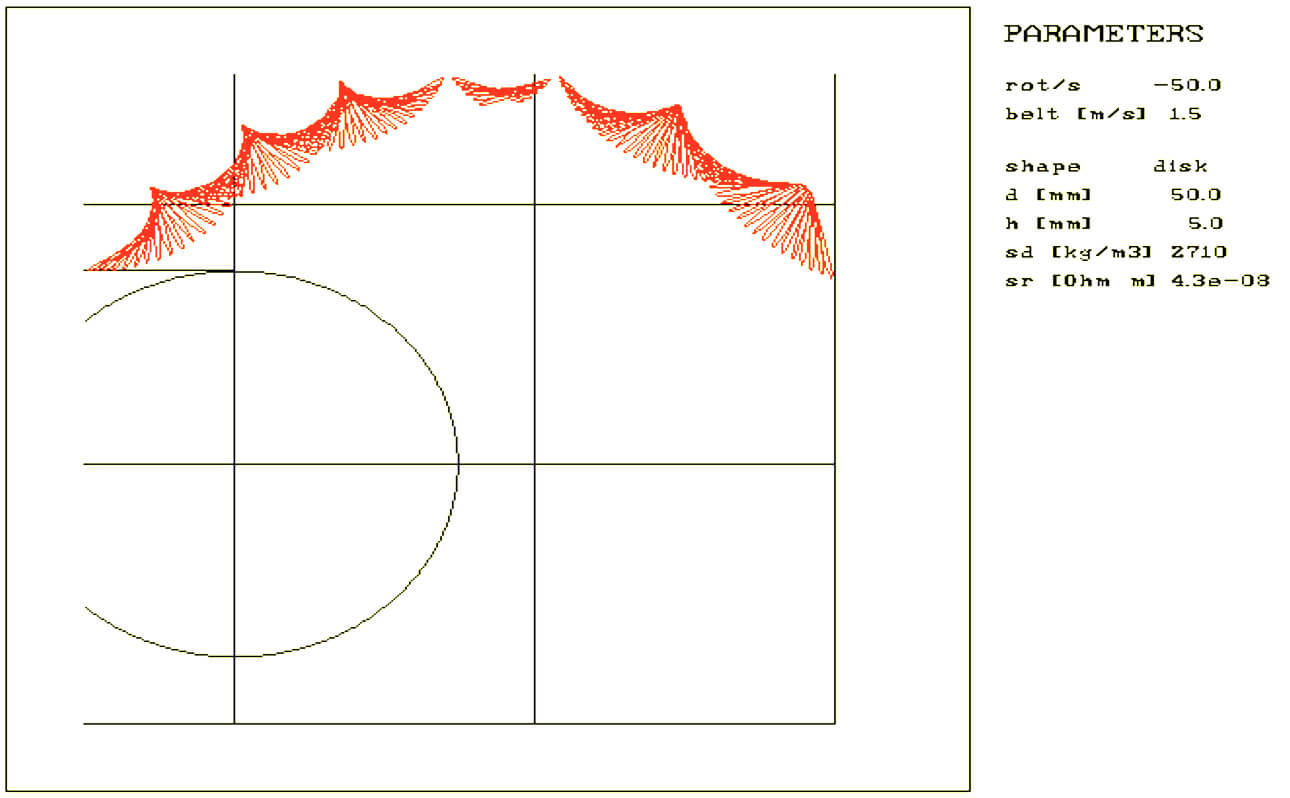
Rotor speed : 3,000 rpm.
Belt speed : 1.5 m/s
Particle : Al disc D50x5 mm.
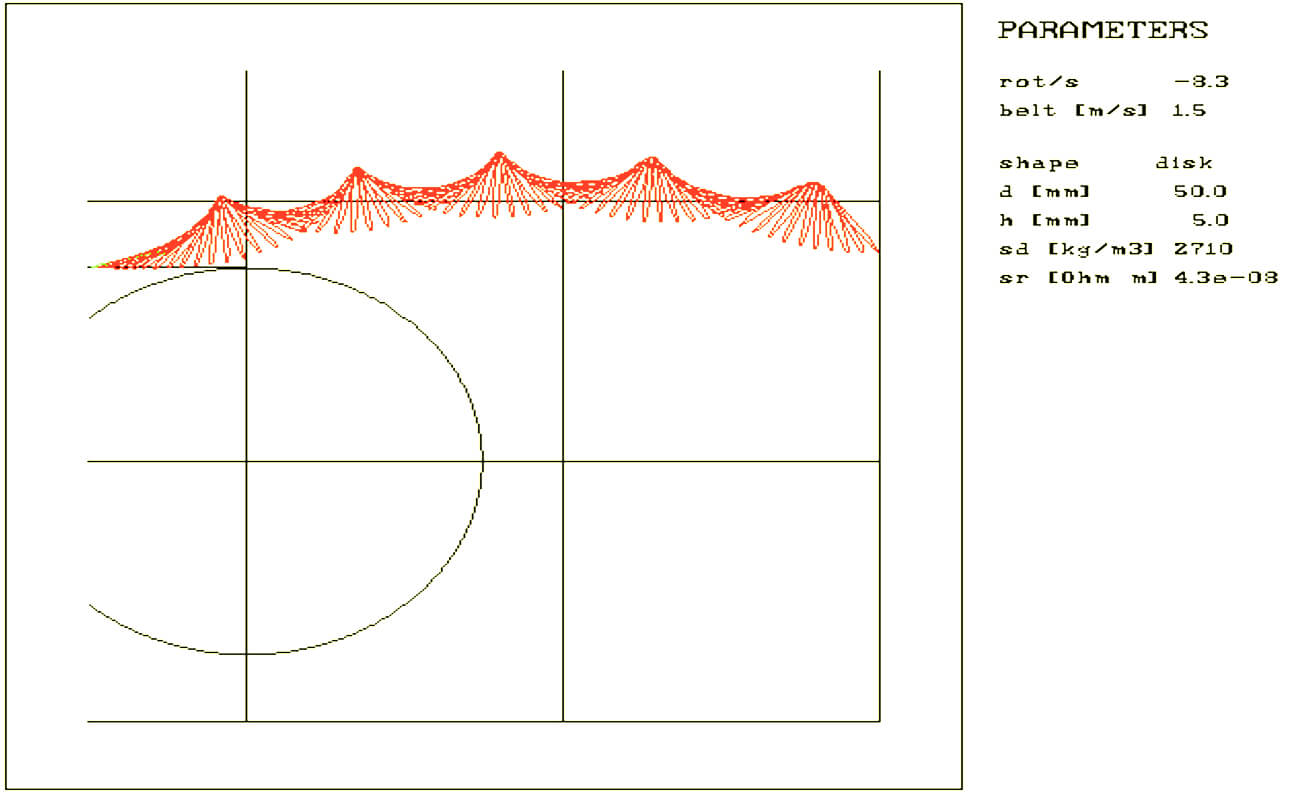
Rotor speed : 500 rpm.
Belt speed : 1.5 m/s
Particle : Al disc D50x5 mm.
3] Rotor rotation direction
The magnet can rotate both in the same direction as the belt (co-rotating) and in the opposite direction (counter-rotating). Normally, a co-rotating direction is always chosen. However, in some cases (for example, with very small particles), a counter-rotating direction is an option.
4] Position of the separation partition
The position of the separation partition is crucial for the effectiveness of the EC separator. Simply put, if you were to place the separation plate against the reversing drum, the recovery would be 100% and the grade 0%. Conversely, if the partition is positioned too far from the reversing drum, the opposite would be true. The position of the partition should be chosen to best meet the intended objectives in terms of grade/recovery ratio.
5] Inclination angle of the separation partition
The inclination angle of the separation partition should be chosen to minimize obstruction.
6] Distribution and layer thickness of the material flow on the conveyor belt (EC)
The input flow should be evenly distributed across the belt to create a well-spread mono-layer.
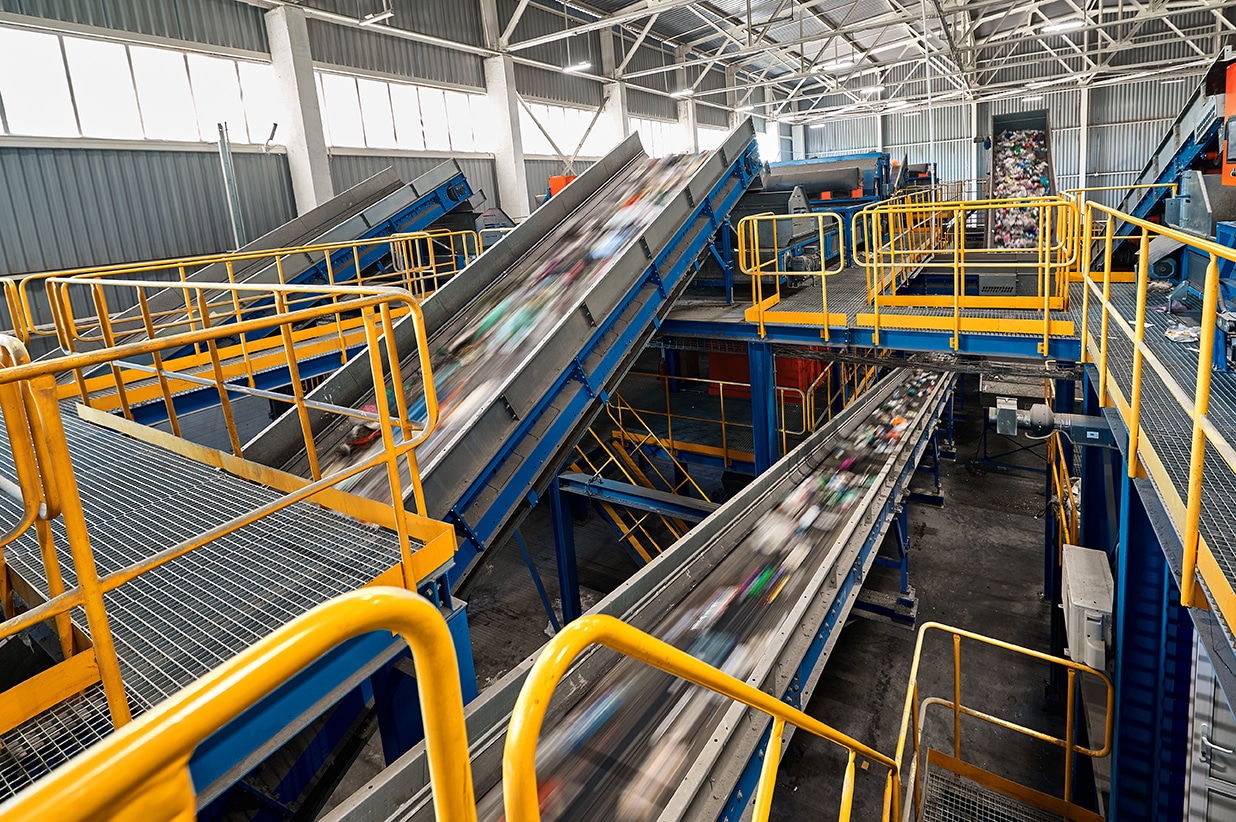
Benefits and Applications
Improved recovery rates
The eccentric Eddy Current separator excels at recovering ultrafine fractions, contributing to higher overall recovery rates in recyclers. To release encapsulated nonferrous particles in your fraction, consider reducing them by using a fine screen size during shredding. These are then reactive in combination with our high frequency rotor and therefore possible to separate.
Reduced Environmental Impact
By targeting and recovering ultra-fine particles, the separator minimizes the environmental impact of discarded materials, promoting sustainability in waste management practices.
Versatility in Material Processing
The adjustable parameters of the separator make it suitable for a wide range of applications, including electronic waste(WEEE), bottom ash (IBA), plastics and fine-grained materials from various industries.
Dutch Magnetics has raised the bar with the Eccentric Eddy Current Separator, offering a specialized solution for the challenging task of separating ultra-fine fractions in recycling processes. This innovative technology not only improves the efficiency of material recovery but also contributes to the broader goals of sustainable resource management. As the industry continues to evolve, solutions like the Eccentric Eddy Current Separator are paving the way for more precise and effective recycling practices.